武汉富士康工厂
2023-02-17 10:16:23 来源: 点击:
为满足客户要求,提高定制化水平,缩短交货周期,富士康武汉工厂大规模引进先进分析和灵活自动化技术,重新设计制造系统,将直接劳动生产率提高86%,质量损失减少38%,交货周期缩短至48小时(缩短29%)。近年来,
为满足客户要求,提高定制化水平,缩短交货周期,富士康武汉工厂大规模引进先进分析和灵活自动化技术,重新设计制造系统,将直接劳动生产率提高86%,质量损失减少38%,交货周期缩短至48小时(缩短29%)。
近年来,富士康武汉工厂以8K+5G图像大数据和工业互联网平台为突破口,大力推进转型创新发展。
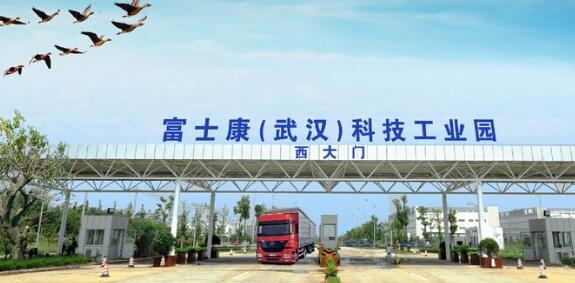
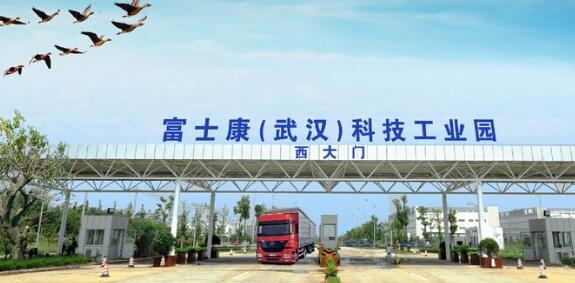
1、注重核心技术研发
工厂拥有高端R&D设计和智能模具开发团队;拥有大型模具、连续模具、精密模具及关键部件、显示模块、大数据与深度学习、人工智能建模等核心关键技术;拥有国际实验认证机构华南检测中心,为产品提供全方位的质量检测。通过核心技术的研发和应用,工厂可以为客户提供创意ID、从设计、模拟仿真到试模量产的个性化定制服务,实现了从客户需求、高科技研发到优质量产的无缝衔接。
二、注重精益生产和智能制造
工厂整合云智慧技术智能制造服务优势,建立图像大数据实验系统,加快自动化和数字化进程。全面引入工业机械人FOXBOT;自主研发全生产自动化、产品测试自动化、光学视觉检测智能化、过程视觉化、信息集成化;大力推进精益生产理念,实现全厂81%以上的自动化。此外,工厂还通过校企合作、行业顶尖企业战略合作等模式,突破技术难点,优化解决方案,搭建全套数字化管理平台。
在走向智能制造的同时,工厂打造了从台式电脑到智能自动售货机、智能大屏幕、高端工作站、人工智能光学智能检测设备、智能手机精密机构的多元化产业布局,产品逐步实现智能化转型。
三、实施人才建设和智能管理
工厂注重人才梯队建设,建设安全、舒适、高效、绿色的文化社区,通过数字技术实现从传统公园向智能公园的转变。引入人脸识别系统,与HRsmart系统连接,实现大数据互联;建立微服务平台,提高业务效率;建立智能安全运营中心,一键联动指挥,消除信息安全死角;利用无限屏幕视频连接,创造高效舒适的会议环境;通过对节能空间的准确分析,实现节能降耗和绿色运营。
四、明确转型创新发展方向
工厂以“云移动大智能网络+机器人”为基本转型政策和战略,实现数据与管理的有机整合,构建云计算、移动终端、物联网、大数据、人工智能、高速网络和机器人技术平台“先进制造+工业互联网”新生态,为华中企业提供新的产品制造和工业互联网综合解决方案,实现智能制造。
通过数字化转型,传统制造业减少了资源消耗和碳排放,提高了生产效率和企业利润,并在富士康武汉的“灯塔工厂”中得到了验证。其成果和实践充分表明,数字化转型不是一个选择题,而是一个不可避免的发展趋势。只有积极接受数字化转型的企业,才能在未来继续保持行业领先地位。富士康武汉工厂以自己的先进模式树立行业基准,促进转型创新发展,引领传统制造企业进入“互联网+制造”的新领域。
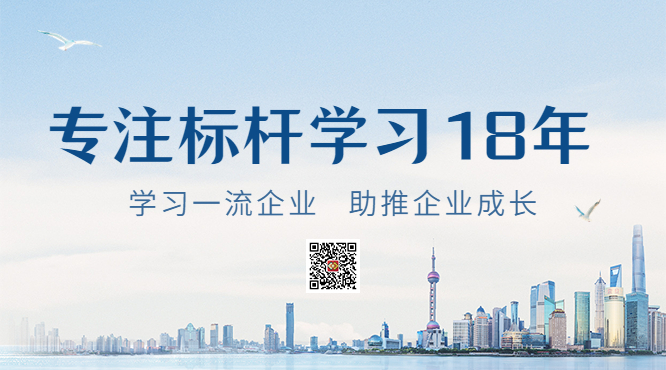
考察研学联系方式/参观预约申请
- 联系电话:010-52463211
- 联系手机:13661395399
- 联系人:万斌老师
考察公开课推荐
- 2025年公开课考察计划
- 2025年11月24-25日 对标阿里巴巴&抖音&网易 学企业出海营销实战
- 2025年8月21-22日 考察领军企业出海秘籍 对标华为、联想、传音 出海实战案例
- 2025年5月12-13日 中国企业出海营销的制胜之道 考察美的、名创优品、希音
- 2025年7月12-13日 北京专场 对标华为、腾讯、京东 学HRBP如何为业务创造价值
- 2025年3月28-29日 上海专场 对标华为、腾讯学HRBP如何为业务创造价值
- 2025年2月21-22日 深圳专场 对标华为、腾讯学HRBP如何为业务创造价值
- 2025年4月21-22日 揭秘品牌背后的创新营销密码 对标小红书、抖音、瑞幸咖啡、东鹏特饮
- 5月19-20日 对标上海星巴克、东鹏特饮、霸王茶姬、泰山原浆 学习智慧零售打造
- 2025年4月28-29日 走进北京阿里&智谱&京东&华为 对标AI赋能企业增长的新纪元