天津丰田对标主题
2019-07-02 12:33:24 来源:王龙 点击:
天津丰田王老师企业运营优化管理实践专家精益工艺设计和质量控制专家项目管理应用和成本控制专家企业管理和技术咨询顾问具备极强的技术和管理经验,已为上百家企业技术人员提供过运营管理、精益工艺技术和质量技
天津丰田 王老师
企业运营优化管理实践专家
精益工艺设计和质量控制专家
项目管理应用和成本控制专家
企业管理和技术咨询顾问
具备极强的技术和管理经验,已为上百家企业技术人员提供过运营管理、精益工艺技术和质量技术相关的培训与咨询。
提出运用精益管理和精益工艺设计思维与精益生产相结合进行企业运营改善,为企业进行量身打造,依据企业实际需求进行专业培训和管理咨询,推动企业从上层管理综合分析,设定合理的运营管理模式和生产技术模式,优化企业管理和体系流程,合理控制企业成本,提升企业运营的价值点,培养专业管理人才和技术人才。
·专业经历:
拥有15年制造业从业经验,其中有10年的生产及精益管理和5年的工艺管理经历。先后在丰田汽车公司担任生产管理职位,在西门子公司负责精益改善和工艺管理,并且在博格华纳汽车部件公司担任生产经理的职务。
拥有丰富的精益管理经验,并且实施和参与过流水线建立等大型精益改善项目;同时拥有丰富的生产管理经验并带领过直接下属超过30人的团队经历。
拥有丰富的工艺技术、项目管理和运营管理经验,多年技术和管理培训以及企业内部咨询经验,对运营管理、项目管理、精益工艺设计和精益生产等方面具有丰富技术实践经验和培训经验;结合国际制造水平和管理体系分析国内企业,推动企业做适合的专用运营管理模式、项目管理模式和精益工艺技术模式。
·擅长领域:
企业精益体系的建立和实施。运营管理和优化设计,结合精益思想对运营系统(计划、采购、物流、仓储、生产等)进行管理实战和质量管控。拥有丰富的丰田管理方法和实践经验。 同时对于西门子数字化和智能制造体系有着深刻的理解和实践经验。
系统化的问题解决方法和实践;
精益工艺设计和管理;
成本分析和优化管理;
企业专用流程体系优化分析;
IE方法研究和培训咨询;
防错设计培训与咨询;
专用生产线建立和规划的咨询;
生产现场精益管理咨询;
在项目管理、SAP系统、自主改善、体系流程设计、顾客审核准备、企业管理、人员结构优化和人才培养等领域也具有丰富的经验。
·主讲课程:
依据企业实际需求独立开发课程,结合实战经验进行专业课设计:
《系统化的问题解决》
《精益价值流程图析-VSM》
《精益基础及理念》
《7大浪费的识别及改善》
《项目管理应用》
《产能与制造成本分析方法》
《FMEA风险分析方法》
《控制计划及管控方法》
《防错设计》
《精益单元设计及人机工程学》
《5S及可视化管理》
《创新型思维》
《现场及车间的精益管理管理》
《标准作业的原则与应用》
《物料的精益管理及看板的应用》
《A3思维方式及实践》
《TPM体系的建立及实践》
《精益行政》
《一线管理人员的管理职责》
《生产计划与物料控制》
《精益流程图》
·技术培训与企业咨询经历:
涉及的企业行业有:汽车、风电、船舶、铁路、铸造、航空航天系统、精密仪器、电气、机械、智能家居、轻工、重工等。
·主要项目经历:
“Milk-run”- 水蜘蛛精益物料配送体系在工厂内的实施;
“SFM”- 精益车间管理体系的实施;
仓库“U”库位布局的精益改善;(BULK / KANBAN的实施)
看板式物料配送方式的导入;
精益柔性生产线方式的建立,提高生产效率;(流水线及单元式布局的导入)
“SMED”快速换型在机加工及装配生产线的成功实施,并进行标准化;
“TPM”体系的导入及成功的实施;(同时包括缺陷红卡/OPL-一点经验)
齿轮马达Flow line-精益流水线的建立及作业三票的建立;(工程能力表/作业组合票/标准作业票)
5S 体系的建立和在工厂内的成功实施;(体系建立/定期检查/持续改善/Chalk circle实施)
“Lean Admin.”精益行政体系的实施及相关改善的跟踪;
公司级VSM-价值流图析的绘制及相关改善行动方案的跟踪及管理;(T.T/C.T/LCD概念的导入)
TOYOTA WAY-问题解决方法在各个车间的导入;(CIP / A3)
·主讲课程建议大纲:
企业运营优化管理实践专家
精益工艺设计和质量控制专家
项目管理应用和成本控制专家
企业管理和技术咨询顾问
具备极强的技术和管理经验,已为上百家企业技术人员提供过运营管理、精益工艺技术和质量技术相关的培训与咨询。
提出运用精益管理和精益工艺设计思维与精益生产相结合进行企业运营改善,为企业进行量身打造,依据企业实际需求进行专业培训和管理咨询,推动企业从上层管理综合分析,设定合理的运营管理模式和生产技术模式,优化企业管理和体系流程,合理控制企业成本,提升企业运营的价值点,培养专业管理人才和技术人才。
·专业经历:
拥有15年制造业从业经验,其中有10年的生产及精益管理和5年的工艺管理经历。先后在丰田汽车公司担任生产管理职位,在西门子公司负责精益改善和工艺管理,并且在博格华纳汽车部件公司担任生产经理的职务。
拥有丰富的精益管理经验,并且实施和参与过流水线建立等大型精益改善项目;同时拥有丰富的生产管理经验并带领过直接下属超过30人的团队经历。
拥有丰富的工艺技术、项目管理和运营管理经验,多年技术和管理培训以及企业内部咨询经验,对运营管理、项目管理、精益工艺设计和精益生产等方面具有丰富技术实践经验和培训经验;结合国际制造水平和管理体系分析国内企业,推动企业做适合的专用运营管理模式、项目管理模式和精益工艺技术模式。
·擅长领域:
企业精益体系的建立和实施。运营管理和优化设计,结合精益思想对运营系统(计划、采购、物流、仓储、生产等)进行管理实战和质量管控。拥有丰富的丰田管理方法和实践经验。 同时对于西门子数字化和智能制造体系有着深刻的理解和实践经验。
系统化的问题解决方法和实践;
精益工艺设计和管理;
成本分析和优化管理;
企业专用流程体系优化分析;
IE方法研究和培训咨询;
防错设计培训与咨询;
专用生产线建立和规划的咨询;
生产现场精益管理咨询;
在项目管理、SAP系统、自主改善、体系流程设计、顾客审核准备、企业管理、人员结构优化和人才培养等领域也具有丰富的经验。
·主讲课程:
依据企业实际需求独立开发课程,结合实战经验进行专业课设计:
《系统化的问题解决》
《精益价值流程图析-VSM》
《精益基础及理念》
《7大浪费的识别及改善》
《项目管理应用》
《产能与制造成本分析方法》
《FMEA风险分析方法》
《控制计划及管控方法》
《防错设计》
《精益单元设计及人机工程学》
《5S及可视化管理》
《创新型思维》
《现场及车间的精益管理管理》
《标准作业的原则与应用》
《物料的精益管理及看板的应用》
《A3思维方式及实践》
《TPM体系的建立及实践》
《精益行政》
《一线管理人员的管理职责》
《生产计划与物料控制》
《精益流程图》
·技术培训与企业咨询经历:
涉及的企业行业有:汽车、风电、船舶、铁路、铸造、航空航天系统、精密仪器、电气、机械、智能家居、轻工、重工等。
·主要项目经历:
“Milk-run”- 水蜘蛛精益物料配送体系在工厂内的实施;
“SFM”- 精益车间管理体系的实施;
仓库“U”库位布局的精益改善;(BULK / KANBAN的实施)
看板式物料配送方式的导入;
精益柔性生产线方式的建立,提高生产效率;(流水线及单元式布局的导入)
“SMED”快速换型在机加工及装配生产线的成功实施,并进行标准化;
“TPM”体系的导入及成功的实施;(同时包括缺陷红卡/OPL-一点经验)
齿轮马达Flow line-精益流水线的建立及作业三票的建立;(工程能力表/作业组合票/标准作业票)
5S 体系的建立和在工厂内的成功实施;(体系建立/定期检查/持续改善/Chalk circle实施)
“Lean Admin.”精益行政体系的实施及相关改善的跟踪;
公司级VSM-价值流图析的绘制及相关改善行动方案的跟踪及管理;(T.T/C.T/LCD概念的导入)
TOYOTA WAY-问题解决方法在各个车间的导入;(CIP / A3)
·主讲课程建议大纲:
课程 | 知识点 | 授课用时(H) | 授课对象 |
精益理念的践行 | 1)精益实施的必要性 | 3 | 企业管理层 / 一线管理者 / 改善工程师 |
2)精益生产概念和起源 | |||
3)丰田精益生产系统的模型(TPS) | |||
4)精益生产对于企业的意义 | |||
5)持续改善的思维 | |||
6)企业管理者如何践行精益 | |||
七大浪费及现场练习 | 1)浪费的定义 | 2 | 管理层 / 改善工程师 |
2)杜绝浪费对于企业的意义 | |||
3)杜绝浪费在现场管理中的实施 | |||
4)如何培养员工建立消除浪费的意识 | |||
5)现场“浪费识别”练习 | |||
5S及可视化的实施 | 1)5S起源及定义 | 2 | 管理层 / 改善工程师 |
2)5S实施的目的及方法 | |||
3)可视化管理的实施方法 | |||
4)5S的收益以及如何在现场实施 | |||
5)可视化的收益以及如何在现场实施 | |||
6)5S现场实践的联系(现场) | |||
系统性问题解决及练习 | 1)问题解决的起源与背景 | 4 | 管理层 / 改善工程师 |
2)丰田工作方法-10大基本意识 | |||
3)关于“问题”的定义 | |||
4)问题解决的步骤 | |||
5)七大质量工具及应用 | |||
6)企业管理者如何建立“问题解决的意识” | |||
7)问题解决的理念对于企业的意义 | |||
价值流分析及练习 | 1)基本定义及原则 | 6 | 一线管理者 / 改善工程师 |
2)精益价值流的目的 | |||
3)价值流的对于企业的重要意义 | |||
4)价值流的绘制步骤 | |||
5)价值流设计及应用 | |||
物料的精益管理 | 1)物料配送原则和方法 | 5 | 一线管理者 / 改善工程师 |
2)物料供给中的浪费识别 | |||
3)精益物料的供应流程及循环取料 | |||
4)看板的概念及应用 | |||
5)平准化生产的概念及生产模型 | |||
6)看板运用的相关计算 | |||
7)XYZ/ABC 管理原则简介 | |||
8)练习-关于特殊物料的配送 | |||
9)低成本自动化的导入 | |||
精益单元设计 | 1)精益单元设计基础 | 4 | 一线管理者 / 改善工程师 |
2)典型的精益单元布局介绍 | |||
3)精益单元典型模型 | |||
4)工位设计的概念 | |||
5)典型案例的分享 | |||
6)精益单元理念的建立 | |||
7)工位设计的实施原则(数据分析) | |||
8)方法及指导原则 | |||
持续改善的企业文化 | 1)工作时间衡量的方法 | 4 | 一线管理者 / 改善工程师 |
2)时间衡量的定义 | |||
3)SMED 定义及必要性 | |||
4)传统换模方式的介绍 | |||
5)SMED 的实施方法 | |||
6)Mock Up 概念及现场实施方法 | |||
标准作业的原则及应用 | 1)标准作业与作业标准的定义 | 4 | 一线管理者 / 改善工程师 |
2)标准作业三要素 | |||
3)标准作业实施的必要性 | |||
4)标准作业制作的方法 | |||
5)标准作业体制的建立 | |||
6)标准作业的练习(录像观察) | |||
A3思维方式及精益实践 | 1)A3报告的概念 | 4 | 企业管理层 / 一线管理者 / 改善工程师 |
2)A3报告的结构 | |||
3)如何利用A3的思维解决问题 | |||
4)如何利用A3的进行沟通 | |||
TPM的实施 | 1)TPM的发展史及模块 | 2 | 一线管理者 / 改善工程师 |
2)TPM的实施的必要性 | |||
3)TPM的七步法及常用工具 | |||
现场管理的实施原则 | 1)现场管理的定义及实施目的 | 3 | 管理层 / 一线管理者 / 改善工程师 |
2)现场管理的5要素(流程管理、沟通与组织、可视化、流程标准化、问题解决及持续改进) | |||
3)领导力原则和管理 | |||
精益行政原则 | 1)精益行政的概念及模型 | 4 | 管理层 / 改善工程师 |
2)方针管理的定义及实施原则 | |||
3)西门子精益生产的机构 | |||
4)精益生产推动的原则(理论) | |||
5)流程图与价值流图的区别 | |||
6)精益行政流程图的绘制方法 | |||
项目管理 | 1)项目管理的定义 | 3 | 改善工程师 |
2)项目进程管理 | |||
3)项目范围管理 | |||
4)人员管理与有效沟通 | |||
5)项目风险管理 | |||
6)项目费用管理 | |||
一线管理人员的职责 | 1)生产线班长的管理职责 | 5 | 一线管理者 |
2)师徒原则的实施方法及苏格拉底提问 | |||
2)成长模型的介绍 | |||
3)职场中的杀手短语 | |||
4)一线班组长的一天 | |||
5)生产线组长的管理职责 | |||
生产计划与物料控制原则 | 1)生产计划在生产过程中的角色 | 3 | 一线管理者 / 改善工程师 |
2)生产计划在生产过程中的角色 | |||
3)企业取料管理的精髓 |
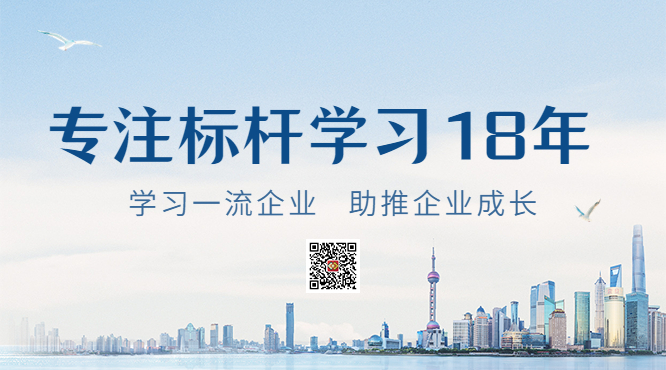
考察研学联系方式/参观预约申请
- 联系电话:010-52463211
- 联系手机:13661395399
- 联系人:万斌老师
考察公开课推荐
- 2025年公开课考察计划
- 2025年11月24-25日 对标阿里巴巴&抖音&网易 学企业出海营销实战
- 2025年8月21-22日 考察领军企业出海秘籍 对标华为、联想、传音 出海实战案例
- 2025年5月12-13日 中国企业出海营销的制胜之道 考察美的、名创优品、希音
- 2025年7月12-13日 北京专场 对标华为、腾讯、京东 学HRBP如何为业务创造价值
- 2025年3月28-29日 上海专场 对标华为、腾讯学HRBP如何为业务创造价值
- 2025年2月21-22日 深圳专场 对标华为、腾讯学HRBP如何为业务创造价值
- 2025年4月21-22日 揭秘品牌背后的创新营销密码 对标小红书、抖音、瑞幸咖啡、东鹏特饮
- 5月19-20日 对标上海星巴克、东鹏特饮、霸王茶姬、泰山原浆 学习智慧零售打造
- 2025年4月28-29日 走进北京阿里&智谱&京东&华为 对标AI赋能企业增长的新纪元